
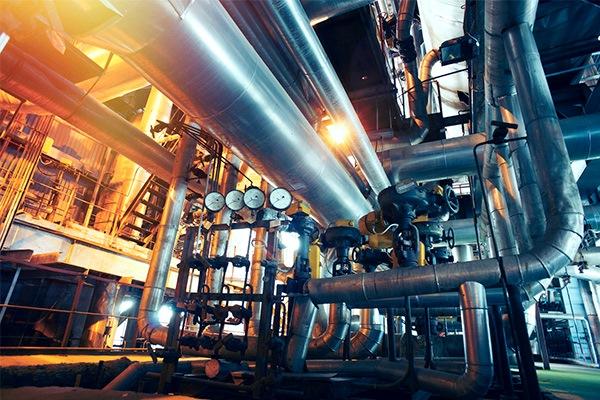
O detector de gás serve para medir e indicar a concentração de determinados gases no ar através de diferentes tecnologias. Normalmente é empregado para impedir a exposição a substâncias tóxicas e incêndio. Detectores de gás são frequentemente operados por dispositivos a bateria e utilizados para fins de segurança. Eles são fabricados como unidades portáteis ou estacionárias (fixas) e unidades de trabalho, indicando altos níveis de gases através de uma série de indicadores visíveis ou audíveis, como alarmes, luzes ou uma combinação de sinais. Embora muitas das unidades antigas de detectores de gás padrão fossem originalmente fabricadas para detectar um gás, modernos dispositivos multigás ou multifuncionais são capazes de detectar vários gases ao mesmo tempo. Alguns detectores podem ser utilizados como unidades individuais para monitorar pequenas áreas de trabalho, ou podem ser combinadas unidades para criar um sistema de proteção.
Como detectores de gás medem uma concentração de gás especifico, a resposta do sensor serve como ponto de referência ou de escala. Quando a resposta dos sensores ultrapassa um nível pré-determinado, um alarme será ativado para avisar o usuário. Existem vários tipos de detectores disponíveis e a maioria tem a mesma função: monitorar e alertar sobre os níveis de gases perigosos. No entanto, quando se considera o tipo de detector a ser instalado, é útil considerar as diferentes tecnologias de sensores.
Detector de gás e suas tecnologias
Os detectores de gás são classificados pelo tipo de gás que detectam: inflamáveis ou tóxicos. Dentro desta ampla classificação, eles estão mais definidos pela tecnologia que usam: sensores catalíticos e infravermelhos detectam gases combustíveis e eletroquímicos, e tecnologia de semicondutor de óxido metal geralmente detectam gases tóxicos.
Medição dos gases tóxicos
Sensores eletroquímicos ou células são geralmente usados na detecção de gases tóxicos como o monóxido de carbono, cloro e óxidos de nitrogênio. Eles funcionam por meio de sinais de eletrodos quando um gás é detectado. Geralmente, esses tipos de detectores são altamente sensíveis e emitem sinais de alerta através de correntes elétricas. Vários fabricantes produzem esses detectores com um display digital.
Semicondutor de Oxido Metal, ou MOS, são também utilizados para a detecção de gases tóxicos (geralmente monóxido de carbono) e trabalham através de um filme sensível a gás composto de estanho ou óxido de tungstênio. O filme sensível reage com gases, desencadeando um dispositivo quando os níveis tóxicos estão presentes. Geralmente, os sensores de óxidos metálicos são considerados eficientes devido a sua capacidade de operar em faixas de baixa umidade. Além disso, eles são capazes de detectar uma série de gases, incluindo combustíveis.
Medição de gases combustíveis
Atualmente o um grande número dos detectores de gás fabricados são os sensores catalíticos. Esta tecnologia é utilizada na detecção de gases combustíveis, tais como hidrocarbonetos, e funciona através de oxidação catalítica. Os sensores deste tipo de detector são tipicamente construídos a partir de uma bobina de fio de platina tratada. Quando um gás combustível entra em contato com a superfície do catalisador, ela é oxidada e a resistência da fiação é alterada pelo calor que é liberado. Um circuito de ponte é normalmente usado para indicar a mudança de resistência.
Sensores infravermelhos ou detectores de IR trabalham através de um sistema de transmissores e receptores para detectar gases combustíveis, especialmente os vapores de hidrocarbonetos. Normalmente, os transmissores são fontes de luz e receptores são detectores de luz. Se o gás está presente no caminho óptico, interferirá com o poder da transmissão de luz entre o emissor e o receptor. O estado alterado da luz determina se e que tipo de gás está presente.
Aplicações comuns de detectores de gás
Embora os detectores sejam uma aplicação essencial para a segurança doméstica e comercial, também são empregados em muitos setores industriais. Os detectores de gás são usados em atividades de soldagem para detectar gases tóxicos e combustíveis e em centrais nucleares, para detecção de gases combustíveis. Eles também são comumente utilizados para detectar vapores perigosos em estações de tratamento de águas residuais.
Os detectores de gás são muito eficientes em espaços confinados, onde não há ocupação permanente do trabalhador. Esses espaços incluem tanques, poços, vasos e caixas de armazenagem. Detectores também podem ser colocados em um local para detectar toxinas antes da entrada dos ocupantes.
Informações adicionais do detector de gás
Embora os detectores de gás geralmente sejam uma tecnologia confiável, com alguns modelos capazes de durar até cinco anos, a sua devida função é geralmente dependente da manutenção do usuário, da inspeção da bateria e da calibração. A calibração é um procedimento executado para garantir a segurança dos detectores estarem medindo o nível correto de gás. Além disso, o tempo de vida dos detectores de gás também depende muitas vezes da quantidade de vapores de gás a que estão expostos. A calibração deve ser frequente, pois sensores contaminados podem não registrar os níveis de gases perigosos.
Antes de iniciar um Teste de Resposta certifique-se que tenha as ferramentas necessárias:
Cilindro de gases com tipo e concentração do gás de teste – Padrão BW 04 gases CO – 100 ppm H2S – 25 ppm %LEL – 50 % vol O2 – 18 % vol Regulador de vazão Adaptador de calibração Mangueira
Um teste de resposta confirma a capacidade do detector de gás responder aos gases alvo. O teste de resposta expõe o detector a concentrações de gás que excedem as definições de alarme confirmando a capacidade do sensor de responder ao gás, portanto consiste em aplicar o gás de referência (span) no equipamento, apenas para verificação da resposta do detector ao contato com os gases, avaliando operação dos alarmes, e se a leitura indicada no display atinge os spans de referência.
Conecte o gás de teste, o regulador, a mangueira de amostragem e o adaptador de calibração. Abra totalmente a válvula do regulador e conecte o adaptador de calibração ao detector. A resposta ao gás de teste deverá ser quase imediata. Se os sensores não responderem, demorarem mais de um minuto para responder ou se as leituras não corresponderem ás concentrações do gás de teste, calibre o detector e faça um novo teste de resposta.
Procedimentos do Bump Test NR33 :
Certifique-se de que a área esteja livre de gases perigosos e zere automaticamente o detector antes do teste. Use apenas gases de testes de qualidade superior ( Cilindros de calibração ) .
Calibração NR33
Passo a passo da calibração dos modelos: GasAlertMicroCLip XT, XL e X3.
A precisão do seu detector de gás é ajustada através da calibração. Uma forma fácil de entender a calibração é dividila em um procedimento de duas etapas. Na primeira etapa, uma leitura de base (zero) é efetuada em um ambiente de ar limpo. Na segunda etapa, os sensores são expostos a concentrações de gases conhecidas. O instrumento usa esta base e a concentração de gás conhecida para determinar a escala de medição da sua resposta ao gás. Importante: Calibre apenas em áreas seguras e livres de gases perigosos. Não calibre o detector durante ou imediatamente após a carga.
Iniciar a calibração Inicie o modo de calibração mantendo pressionado o botão de comando para desativar o detector. Continue a manter o botão pressionado quando a unidade ler “DESLIGA” e após o instrumento ter concluído o desligamento. O display LCD fica em branco por um breve período, depois o detector inicia a contagem regressiva da calibração.
Não solte o botão de comando até a contagem regressiva ser totalmente concluída e o detector começar o procedimento de auto zero.
Durante o auto zero, o detector define sua base em um ambiente de ar limpo e fresco, onde as leituras esperadas são iguais a 20,9% para oxigênio, 0% LEL para gases combustíveis e 0 ppm para gases tóxicos. Como uma precaução de segurança, o detector avisa sobre uma mensagem de erro se a definição zero (base) Parecer estar fora do nível esperado de parâmetros predeterminados. Após zerar os sensores, você será aconselhado a aplicar o gás de calibração.
Aplicar o gás com cilindro de referência (NR 33)
Certifique-se de que tenha o tipo e as concentrações adequadas de gases, tubos de amostragem, reguladores e adaptador de calibração. Ter as ferramentas corretas é fundamental para uma calibração precisa. Verifique todas as conexões entre o gás de calibração, o regulador, a mangueira de amostragem e os encaixes de conexão rápida. Quando solicitar a aplicar gás, abra totalmente a válvula do regulador e conecte o adaptador de calibração ao detector.
Verifique todas as conexões entre o gás de calibração, o regulador, a mangueira de amostragem e os encaixes de conexão rápida. Quando solicitar a aplicar gás, abra totalmente a válvula do regulador e conecte o adaptador de calibração ao detector.
Obs: Use apenas gases de calibração de alta qualidade e rastreáveis.
Span automático (NR33)
O diagnóstico de Span automático do detector verifica se os níveis do gás de calibração detectados correspondem aos níveis previstos. Se 50% do valor esperado for atingido em 30 segundos, o detector emitirá um bipe e continuará o span. Um Auto Span completo dura aproximadamente dois minutos. Depois de concluído, o detector avisa quando vence a próxima calibração.
Calibração, teste de resposta e Bump-Test, definições (NR33)
Calibração NR33
De acordo com o a Portaria n° 232 de 08/05/12 – Vocabulário Internacional de Metrologia (VIM), “calibração é o conjunto de operações que estabelece, sob condições especificadas, a relação entre os valores indicados por um instrumento de medição e os valores correspondentes das grandezas estabelecidas por padrões”. Desta forma calibração é a relação entre o valor indicado pelo detector e o valor do padrão de gás. Através desta operação, pode-se estabelecer o “erro de medição” do detector de gás. No VIM, “erro de medição é definido como sendo a “Diferença entre o valor medido duma grandeza e o valor de referência”. Se houver internamente um critério ou limite de erro permissível para erro de medição apresentado e, caso o erro for superior ao limite, se faz necessário um ajuste no instrumento, ou seja, o “conjunto de operações efetuadas num sistema de medição, de modo que ele forneça indicações prescritas correspondentes a determinados valores duma grandeza a ser medida”.
Teste de resposta ou Bump Test (NR33)
São termos que o mercado instituiu, baseados na definição de “verificação de um instrumento de medição” da Portaria INMETRO n° 163 de 06/09/2005 (Vocabulário Internacional de Termos de metrologia Legal), conforme definido no item 3.12: “Procedimento que compreende o exame, a marcação e/ou a emissão de um certificado de verificação e que constata e confirma que o instrumento de medição satisfaz às exigências regulamentares”. Interessante observar que o teste que o profissional realiza antes do uso do equipamento para verificar a condição de funcionamento do detector de gases, confirmando a capacidade do instrumento em responder aos gases-alvo é conhecido como Teste de resposta/Bump Test e, em alguns casos, ambos os termos são utilizados no mercado como sinônimo de calibração.
Frequência de envio de detectores de gases para calibração NR33
Este tema é polêmico, muitos profissionais tem dúvidas a respeito da periodicidade exigida para realização da calibração em laboratório, e as dúvidas surgem justamente pela norma regulamentadora, NR-33, não definir um prazo de retorno ao laboratório para nova calibração. No entanto, o Vocabulário Internacional de Termos de metrologia legal define no item 3.16 a Verificação Periódica como “verificação subseqüente de um instrumento de medição efetuada periodicamente em intervalos de tempo especificados e segundo procedimentos fixados por regulamentos”. Portanto, a responsabilidade por assegurar que o equipamento esteja em condições de utilização (funcionamento de todos os recursos) é da empresa, segundo seus procedimentos internos ou recomendações do fabricante presentes no manual de instruções. Nesse respeito, entende-se que a responsabilidade pela definição do intervalo de calibração, aprovação dos resultados expressos no certificado de calibração e aprovação do equipamento para uso é da gestão da segurança da empresa, que através de seus procedimentos e política de segurança determina o intervalo de verificação e/ou calibração na análise da atividade, nos riscos envolvidos e no histórico das condições de trabalho.