
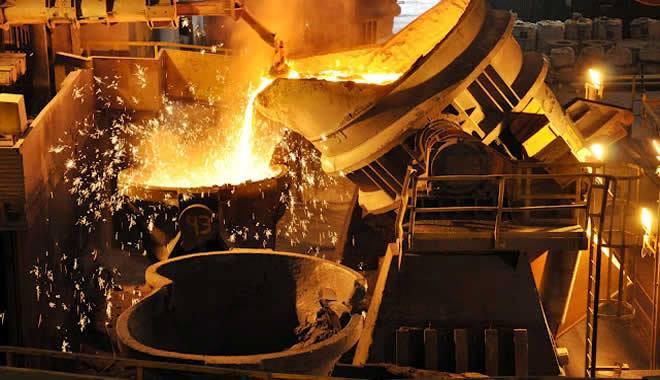
É incontestável a importância que a indústria siderúrgica tem na economia e no desenvolvimento de uma nação. Muitas vezes pioneira na aplicação de novos produtos e processos, ainda guarda métodos de operação seculares. Destaca-se também dentro da fabricação do aço, a atuação dos profissionais da área de saúde e segurança do trabalhador que diariamente vencem desafios de proporções gigantescas.
O aço está presente em quase todas as atividades diárias da humanidade, seja no transporte, comunicação, utensílios domésticos, lazer. Quase tudo que se utiliza pode ter algo ligado a esta tão importante indústria.
Por se tratar de um conjunto de vários métodos produtivos diferentes, a indústria do aço é também um dos mais ricos campos para aprendizado e desenvolvimento em Higiene Ocupacional.
Do recebimento de matérias primas até a laminação de placas, encontramos os mais diversos tipos de agentes químicos, físicos e biológicos, nas mais diversas formas de exposição, obrigando os profissionais da área de saúde e segurança a se aprimorarem continuamente.
Para que as avaliações e intervenções surtam os efeitos desejados, é extremamente importante que se conheça os processos produtivos e todas as suas nuances, afim de identificar de maneira clara e objetiva as ações a serem tomadas no sentido de buscar a melhoria das condições de trabalho.
Dividida basicamente em 5 fases de produção (Preparação da carga – Redução – Refino – Lingotamento – Laminação) o processo de transformação do aço é um vasto campo de atuação para os higienistas ocupacionais. Além dos estágios citados anteriormente, não se pode esquecer da área de Carboquímicos, que tem, na grande maioria das usinas siderúrgicas, papel comercial e industrial de elevada importância.
Em seguida falaremos sobre as principais exposições ocupacionais as quais os profissionais de saúde e segurança do trabalho devem estar atentos na indústria siderúrgica, entretanto, é importante salientar que este material não esgota todas as possibilidades de exposições, cabendo a cada profissional responsável, investigar e indicar os agentes e suas fontes.
Preparação da carga
Recebimento e estoque de matérias primas
Normalmente se recebe os minérios, cargas, fundentes e combustível (carvão mineral) via transporte ferroviário, realizado na maioria das vezes por empresas especialistas neste tipo de movimentação, entretanto, movimentações internas podem ser necessárias através do uso de vagões e locomotivas operadas por colaboradores próprios das usinas, levando a necessidade de avaliações de vibrações as quais esses trabalhadores possam estar expostos. Este mesmo tipo de operação leva a exposição a ruído, provenientes dos motores, deslocamento sobre os trilhos e engate de vagões, além das sirenes de indicação de movimentação.
Ainda nesta área, pode ser necessária a avaliação de poeiras minerais, durante a movimentação das pilhas, assim como a exposição ao calor, devido a grande maioria das atividades serem desenvolvidas a céu aberto. Uma atenção especial deve ser dada as atividades de recebimento e movimentação de carvão mineral, uma vez que o mesmo é citado na NR-15 – Anexo 13.
Além desses fatores, é importante salientar que, em alguns casos, a movimentação, estocagem e distribuição do coque produzido nas coquerias também é de responsabilidade deste setor, o que leva a possíveis exposições a hidrocarbonetos tanto aromáticos polinucelados.
Nos casos onde se recebe sucatas para adição na Aciaria, é necessário um cuidado adicional para evitar o recebimento de materiais radioativos, sendo necessária a implantação de sistemas de controle específicos. É preciso também classificar adequadamente as peças recebidas que ainda estejam com resíduos de tintas, pois, no momento de corte dessas peças pode ocorrer o desprendimento de contaminantes provenientes da composição da tinta aplicada sobre a peça.
Sinterização
Este processo, tem a finalidade de preparar a carga que será transformada em ferro gusa. Esta preparação consiste em aglomerar a quente das misturas de finos de minério, coque e fundentes, resultando em um subproduto denominado “SINTER”. Trata-se de um material com propriedades mais adequadas para operação nos Altos Fornos.
Após a passagem pelos britadores e peneiras, os materiais com granulometria mais baixa são dosados no misturador, sendo aglomerados com adição controlada de água. O material aglomerado é distribuído na esteira de sinterização e passa por um forno com temperatura aproximada de 1200°C. Após este processo, o Sínter passa pelos processos de britagem e resfriamento, para posterior envio aos pátios de matérias primas que farão o abastecimento dos Altos Fornos.
No processo de sinterização, pode-se destacar as exposições a ruído, proveniente dos equipamentos produtivos em geral, calor, advindo do forno de sinterização, esteira de sínter e resfriador. Para os agentes químicos pode-se considerar as exposições a particulados, tanto poeira respiráveis quanto metais, além do óxido de cálcio, todos provenientes da movimentação e dosagem de matérias primas.
Em quase todos os processos de transformação do aço faz-se necessário avaliações investigativas e quantitativas a respeito da presença de Sílica Livre Cristalina, principalmente para não deixar de atender ao Anexo 12 da NR-15.
Coqueria
O setor de Recebimento e Estoque de Matérias Primas é responsável pelo envio do carvão mineral normalmente recebido via transporte ferroviário para o processo de coqueificação. O material passa por dosagem e britagem afim de atingir granulometria adequada para ser submetido a destilação sem presença de oxigênio em temperaturas de aproximadamente 1300°, que, dependendo da eficiência do processo, pode durar até 20 horas. O material é carregado pelo topo de fornos verticais, e após o período de coqueificação, onde se retira os materiais voláteis, ocorre o desenfornamento através da inserção de um embolo empurrado pelo carro de desenfornamento, que com o auxílio de um carro guia, deposita o coque incandescente no carro de apagamento, que por sua vez, conduz este material em brasa até a torre de apagamento, onde se utiliza de jatos d´agua para extinção do material que ainda esteja incandescente. Algumas usinas utilizam o sistema de apagamento ascendente, que consiste em bascular o coque em brasa em um foço, onde a queda livre fará a extinção do material.
Após o apagamento do coque incandescente, ele pode voltar ao setor de Recebimento e Estoque de Matérias Primas para posterior abastecimento do Alto Forno. No processo de coqueificação, além do coque a ser utilizado como combustível para redução de minérios nos Altos Fornos, também é gerado o chamado Gás de Coqueria, um subproduto rico em hidrocarbonetos, e que se tratado corretamente, pode gerar receitas através da comercialização de seus destilados. Esses gases são coletados no topo dos fornos de coque e enviados ao setor de Carboquímicos (falaremos mais adiante sobre este processo), responsável pela destilação e recuperação de substâncias de interesse industrial. Após a limpeza, o Gás de Coqueria pode gerar energia para as demais unidades de produção da usina.
Quando se fala em Higiene Ocupacional em uma coqueria, destaca-se o Ruído, proveniente dos equipamentos produtivos, o calor, proveniente dos fornos de coqueificação, vibrações nos operadores de carro de enfornamento, desenfornamento, carro guia e locomotiva. No tocante aos agentes químicos, uma atenção redobrada é necessária sobre os hidrocarbonetos aromáticos (BTXE) e polinucelados (HAP), mas sem deixar de lado o Monóxido e Dióxido de Carbono. Ainda na esfera dos agentes químicos, vale lembrar as exposições a particulados, alcatrão, amônia e ácido cianídrico, todos esses provenientes do processo de destilação do carvão.
Em se tratando de hidrocarbonetos, deve-se chamar a atenção para o atendimento a Anexo 13 da NR-15, com importância fundamental para o Anexo 13A, suas portaria e Instruções Normativas, que tratam da exposição ocupacional ao Benzeno.
Algumas usinas se utilizam de coqueria com sistema de produção que não destilam os gases provenientes da coqueificação. Neste tipo de processo, conhecido com Heat-Recovey (Suncoque), os gases gerados no interior de fornos são reaproveitados na queima do carvão, eliminando a geração de hidrocarbonetos. Outro detalhe importe que ajuda no controle das exposições ocupacionais, é o fato de que, neste tipo de forno, a pressão é negativa, ou seja, quando o mesmo é aberto para desenfornamento, não há emissões fugitivas, pelo contrário, existe sim uma pequena formação de fluxo de ar de fora para dentro do forno, eliminando assim a exposição dos trabalhadores às substâncias geradas na produção de coque.
Carboquímicos
A unidade de Carboquímicos é responsável pelo tratamento e limpeza do Gás de Coqueria, recuperando diversos coprodutos de interesse industrial.
Uma planta de Carboquímicos, dentro de uma usina siderúrgica, pode ser dividida em: Limpeza de Gases – Remoção de Amônia – Óleos Leves – Dessulfuração – Destilação de Alcatrão. Tendo como principais produtos obtidos o: Benzeno, Tolueno, Xileno, Piche, Naftaleno, Naftas e Óleo Creosoto, todos estes com importantes interesses industriais.
Mais uma vez se destaca as exposições ocupacionais aos Hidrocarbonetos, que estão presentes em todo o processo de remoção e tratamento de gases, principalmente nas coletas de amostras para análise, e devido as suas particularidades, estes agentes ocupacionais devem ter total atenção dos higienistas. Além dos Hidrocarbonetos, pode-se encontrar também, exposições Amônia e Cianetos.
Redução
- Alto forno
Os Alto Fornos são responsáveis pela redução de minério de ferro em ferro gusa, para posterior envio e tratamento na Aciaria. Após a devida preparação, os minérios de ferro, fundentes, sínter e coque são carregados no topo do Alto Forno, enquanto na sua base são injetados partículas de carvão com granulometrias baixíssima (finos de carvão) que, em contato com o ar quente proveniente dos regeneradores e com o coque adicionado no topo, gera gases de elevada temperatura que reagem com a carga de minério, reduzindo o minério de ferro à ferro gusa, que por sua vez, é vazado na base do Alto Forno, através dos furos de vazamento e canais de corrida, sendo o ferro gusa encaminhado para os carros torpedo (ou panelas) e a escória conduzida até o granulador de escória, podendo ser utilizada nas indústrias de cimento.
Os profissionais de saúde e segurança dessas áreas, no tocante a higiene ocupacional, estão sempre atentos aos riscos de exposição a Ruído, principalmente na área das ventaneiras, Calor no furo e vazamento dos fornos, assim com a Particulados de Metais, Monóxido e Dióxido de Carbono, Sulfeto de Hidrogênio e Dióxido de Enxofre.
Refino
- Aciaria
Esta área é responsável pela transformação do ferro gusa, proveniente dos Altos Fornos em Aço, através de tratamento térmicos e químicos.
Após a dessulfuração (redução dos níveis de enxofre), o ferro gusa é transferido para a panela de gusa na Aciaria, onde se normalmente realizada uma amostragem para determinação das propriedades físico-químicas, além da retirada de escória remanescente no skimer. Utilizando-se de pontes rolantes, a panela de gusa é descarregada dentro dos convertedores, equipamentos estes, responsáveis pela transformação de ferro gusa em aço, que se dá pela injeção de Oxigênio que atuará na oxidação do Silício, Manganês, Enxofre, Fosforo e Carbono. Em seguida, é feito um sopro de gás inerte (Argônio) para aumentar a interação do Oxigênio e elevar a eficiência da descarbonização. Em seguida, podem ser necessários ajustes químicos com ferro-ligas para adequação final do tipo de aço que está sendo produzido.A próxima etapa na Aciaria, é o Refino Secundário, onde são realizados os últimos ajustes químicos e térmicos antes do lingotamento.
Considerando as questões das exposições ocupacionais, na Aciaria, os higienistas trabalham no controle das exposições a Ruído, gerados pelos equipamentos industriais em geral, assim como ao Calor, nas atividades de ajustes químicos, coletas de amostras, movimentação de gusa e aço, além é claro das Vibrações, principalmente nos operadores de ponte rolante. Para os agentes químicos, é importante olhar mais de perto os Particulados de Metais, assim como o Monóxido e Dióxido de Carbono.
Lingotamentos
Em seguida ao tratamento final do aço, o mesmo é transferido para a área de lingotamento, com o intuito de conformar o aço em placas para posterior laminação, seja na própria usina ou em seus clientes.
O aço no interior da panela é transferido para o distribuidor, que através de um fluxo continuo, abastece os moldes dotados de resfriamento controlado para conformação das placas. De acordo com as especificações necessárias, as placas são cortadas (oxi-corte) e identificadas automaticamente para posterior encaminhamento ao pátio de placas ou laminação. Dentro os riscos ocupacionais deste setor, podemos destacar mais uma vez o Ruído e o Calor.
Laminações
As placas de aço são posicionadas no interior dos fornos de pré-aquecimento, com a finalidade de preparar as placas para conformação mecânica.
Após a saída do forno, as placas são transferidas para os laminadores onde, de acordo com as necessidades, serão conformadas nas especificações indicadas para cada uso.
Os principais riscos ocupacionais são o Ruído, causado pela movimentação das placas e Calor, advindo do forno e das placas aquecidas. Dependendo do tipo de tratamento que será dado ao aço, avaliações de Metais podem ser necessárias.