
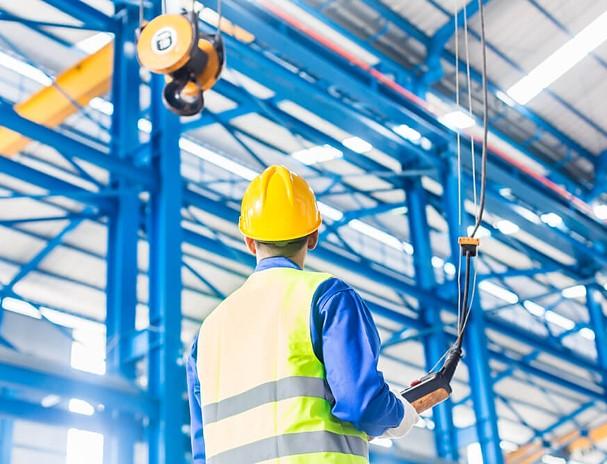
Uma das problemáticas das organizações para a correta aplicação da Segurança e Saúde no Trabalho (SST) passa por uma escolha estratégica na adequação para a sua implementação.
Cada organização utiliza a sua estratégia para uma correta aplicação da SST, sendo tal, o reflexo da sua escolha consoante os processos e condições de trabalho de cada uma delas. Porém, em muitos casos, esses sistemas são pouco funcionais e de difícil implementação.
A filosofia Lean pode ser uma notável solução de aplicação de SST no âmbito de melhoria contínua, podendo alcançar a participação de todas as Partes Interessadas na procura de recursos que permitam desenvolver o trabalho com mais eficácia e eficiência no campo de ação da segurança.
O pensamento Lean comporta um conjunto de práticas que permitem a eliminação de desperdícios, e por consequência um melhor desempenho. Estes desperdícios podem ser considerados na SST, tudo o que seja indesejável, nomeadamente acidentes de trabalho e doenças profissionais que levam a uma redução significativa de custos nas organizações. A prevenção de acidentes, lesões e doenças ocupacionais não só reduzem os custos inerentes ao tratamento e acompanhamento destes efeitos, como transpõem a uma diminuição das paragens no ciclo de produção.
A aplicação desta filosofia permite com maior clareza atingir as metas pretendidas, começando por uma avaliação da situação atual (estado zero), prosseguindo para uma cuidada pesquisa das causas-raiz que provocam as situações indesejáveis, traçar um plano de ação para a sua implementação, seguindo para uma verificação e estandardização e por último à reiniciação inevitável do ciclo.
Os seguintes pontos apresentam uma adaptação dos cinco princípios de atuação do Lean segundo Lean Thinking (Womack et al., 1996), no campo de ação da Segurança e Saúde no Trabalho:
- Definir Valor na perspetiva da compensação que recebemos em troca (Custo Vs Benefício);
- Mapear todos os passos independentemente do valor acrescentado;
- O Movimento Flow (contínuo) dos procedimentos operacionais/funcionais e as suas informações que fluem do início até ao fim de todos os processos;
- Atuar consoante a Necessidade de cada organização;
- A Perfeição através da eliminação completa do desperdício, com o objetivo de valorizar as atividades desenvolvidas na organização.
O Ciclo PDCA vulgarmente conhecido por ciclo de melhoria contínua é considerado uma das ferramentas Lean mais aplicadas às organizações. Este ciclo, idealizado por Walter A. Shewhart (1861-1967) na década de 20 e publicado pela primeira vez em 1939, foi introduzido no Japão após a 2ª guerra mundial, e divulgado por W. Edwards Deming a partir da década de 1950. O Ciclo de Deming, como ficou conhecido, também designado por PDCA (Plan, Do, Check e Act) consiste em planear, executar, avaliar e atuar. Estes elementos pretendem inovar corretivamente e/ou preventivamente de modo que a organização possa obter resultados cada vez melhores, relativamente aos seus indicadores de SST. Esta metodologia utiliza o processo de aprendizagem de um ciclo para aperfeiçoar e adaptar o ciclo seguinte e assim sucessivamente. Trata-se de um processo dinâmico que está sujeito a uma verificação cíclica, onde para além do cumprimento, é também avaliada a eficácia das ações corretivas implementadas.
A presente metodologia segue um desenvolvimento do ciclo PDCA envolvendo o seu processo de implementação com maior detalhe e direcionado a todos os operadores, serviços de suporte, stakeholders e direção. Esta ferramenta está disposta em 11 passos aplicados do seguinte modo:
– Envolvimento direto de todas as Partes Interessadas;
– Análise de uma pequena área, em profundidade;
– Rápida aplicação (duração: 1 semana, no máximo);
– Com orientação para o processo (implementação imediata das melhorias);
– Com orientação para os resultados (resultados quantificáveis e visíveis de imediato);
– Estruturados e normalizados em 11 passos.
5W2H
Esta ferramenta é referenciada na antiguidade como heptágono de perguntas e respostas essenciais par a compreensão do tema: Quem, o quê, onde, quando, porquê, como e quanto custa. Este utensílio apoia essencialmente na fase de definição do tema/problemática e cria uma plataforma comum de entendimento a toda a equipe de qual o problema. Na fase de descrição das soluções serve para reconhecer o que vai ser feito no tempo, no espaço e no domínio do custo bem como a respetiva fundamentação.
Árvore Causal
As árvores causais reconhecem de modo lógico a relação de causa/efeito. Esta ferramenta consiste numa identificação mais completa das causas que confluem para a problemática sendo frequente uma aplicação desta metodologia em indústrias com elevado número de incidentes, pretendendo esclarecer as causas que provocam os mesmos. Estas árvores potenciam um sistema integrado e sistematizado, no reconhecimento dos fatores de risco da atividade em análise, que interagem entre si, possibilitando compreender as causas que dão origem aos incidentes. Dependendo da situação em questão podem tornar-se complexas pois a mesma causa pode incitar mais que um efeito.
BrainStorming
Esta ferramenta não tem uma linha de direções aceites para passos específicos a implementar, sendo que se comporta essencialmente em:
– Desenvolver um enunciado da problemática existente;
– Seleccionar um grupo de participantes (até 12 no máximo);
– Desenvolver o problema num quadro visível a todos os participantes;
– Abordar as 4 regras principais do brainstorming (Críticas são rejeitadas; criatividade é sempre bem-vinda; maior número de ideias apresentadas; combinação de ideias entre participantes).
– Apontar todas as ideias;
– Duração da sessão (cerca de 30 min);
– Seleccionar um grupo para avaliar as ideias;
– Fornecer a lista de ideias ao grupo de trabalho do projeto.
A3
O relatório A3 é um utensílio de suporte à metodologia PDCA anteriormente abordada, com o objetivo de sintetizar o conhecimento, focar toda a equipe, incentivar o diálogo entre todos os intervenientes e fomentar a aprendizagem. Esta ferramenta é exposta fisicamente numa folha de papel, disponível a todas as Partes Interessadas, com as dimensões 40×30 [cm] que lhe dá o nome de A3.
Não existe nenhum modelo específico, contudo apresento de seguida um exemplo possível.
Gestão Visual
Esta será uma das ferramentas do Lean que mais se adequa à Segurança e Saúde no Trabalho, sendo composta por três grandes objetivos:
– Tornar os problemas visíveis;
– Ajudar a manter o contacto com a realidade;
– Exibir e esclarecer o alvo ou a meta a cumprir.
Para além de ser um utensílio de grande aplicabilidade à SST, comporta uma simples e económica implementação nos diferentes tipos de categorias, como por exemplo:
– Etiquetagem de objetos e áreas industriais;
– Indicação visual do comportamento dos equipamentos através de sistemas luminosos;
– Exposição visual de resumos de instruções de trabalho;
– Exposição visual dos indicadores de produtividade KPI através de quadros;
– Promoção do processo de melhoria contínua através de quadros com “before/after”
A correta implementação da presente ferramenta passa por uma persistência da limpeza no local de trabalho promovendo uma clara observação dos problemas.
5S
A metodologia 5S pretende criar e manter um ambiente de trabalho limpo e organizado, sendo estruturado por 5 etapas, nomeadamente:
1S (Seiri): Descartar tudo o que se considera desnecessário no local de trabalho, como ferramentas inúteis ou em duplicado e materiais ou stocks desnecessários;
2S (Seiton): Organizar todo o restante de forma que se localize no sítio ideal para uma correta e fácil laboração no trabalho;
3S (Seiso): Limpar todo o local e Equipamentos de Trabalho. Manter os espaços isentos de obstáculos suscetíveis à promoção de incidentes.
4S (Seiketsu): Padronizar todas atividades que são necessárias para manter a situação actual;
5S (Shitsuke): Manter/Respeitar através de auditorias periódicas evitando o regresso à situação inicial.
Gestão do Desempenho (KPI)
A Gestão do Desempenho é um processo contínuo que define as metas a cumprir de modo a que cada função esteja em condições de poder contribuir para os resultados desejados.
Com base em alguns indicadores de produtividade da organização, a Gestão de Topo deve utilizar uma árvore de Key Performance Indicator (KPI) para os decompor e conceder a cada nível organizacional. Estes objetivos propostos devem ser ambiciosos, mas de aplicação real.
Para uma boa monitorização da eficiência do desempenho de cada função ou departamento organizacional é fundamental a prática de reuniões entre os vários intervenientes com o objetivo de apresentar medidas corretivas para colmatar as metas não alcançadas.
Através de uma breve síntese de ferramentas supracitadas do Lean é possível evidenciar uma relação profunda com a gestão da Segurança e Saúde Ocupacional, promovendo às organizações uma constante prevenção através da minimização de exposição do risco dos trabalhadores nas suas atividades laborais diárias.
A filosofia Lean alcançou uma enorme expansão em todo o mundo do sector industrial sendo aplicada em várias organizações de renome internacional, tais como a Toyota, a Dell e a Zara que conseguiram demonstrar ganhos significativos através da implementação deste conjunto de metodologias organizacionais.
Uma organização segundo a linha de orientação Lean cria um valor acrescentado a todas as Partes Interessadas através de um contributo de trabalho em equipa, no sentido de proporcionar o seu desenvolvimento numa perspectiva de melhoria contínua.
Por: João Calado
Engenheiro Civil e Mestre em Segurança e Higiene no Trabalho